From: Rhonda.D.
Date: 02-28-2005, 09:22 PM (1 of 9)
My machine keeps jamming, with the thread getting stuck around the part that the bobbin race fits into, I have tried cleaning it myself and have not been able to fix the problem so I want to have my machine cleaned and oiled and the one sewing store I asked about a price was $80 Canadian and could do it in 3 days and then I called an independent servicer and he was $60 can. but took 1 week. The machine is a Limited Edition Kenmore 100 stich Are these prices reasonable? Thanks for any input Rhonda |
User: Rhonda.D.
Member since: 02-13-2005 Total posts: 8 |
From: paroper
Date: 02-28-2005, 11:14 PM (2 of 9)
I don't know what the conversion rate is US to Canadian but if that were US, those prices might be rather middle of the road. I paid 50 US for basic care for my sewing machine, but ended up paying 100 for my serger because it took so much longer. That was just before my dealer raised his prices. He is now closer to $80. It is money well spent, however. When you go in, be sure and take the bobbin case so that he can do an adjustment on those. My dealer has a gizmo to check and help adjust the case that we don't have access to. It sounds like you might need a little work on the case to get it back into proper adjustment. You might either ask him to take time to record your serial number on your contract or you might record it. My dealer does this as a matter of routine to protect both of us. A few dealers have been known to switch machines while they are working on them...just a little extra precaution that probably is not needed, but will make you feel a little reassured. At the same time, it protects the dealer from false accusation. When your machine comes back, it should be sewing soooo smooth. It always amazes me that even with careful maintance at home, they always sound quieter and smoother when they come back from the shop.
pam
Bernina 200e, Artista V5 Designer Plus, Explorations, Magic Box, Bernina 2000DE & 335 Bernette Serger, Bernina 1530 Sewing Machine, Bernina 1300 DC Overlock (with coverstitch) |
User: paroper
Member since: 02-03-2004 Total posts: 3775 |
From: Sancin
Date: 03-01-2005, 02:21 AM (3 of 9)
Rhonda - prices quoted for a tune up are the same as I pay here in Prince George, BC. I was surprised to find I liked the independant dealer better (even in his old garage shack full of lots of old machines) as he has dealt with every kind of machine going. I had previously taken my Elna (most current Kenmores are Janome which is related to Elna) into 2 dealer shops and they could not find the problem. This question of jamming came up somewhere else on this discussion list in relation to threads but can't recall what section so search each discussion list. The jamming, I was told was related to how the thread comes off the spool and whether you are using a verticle or horizontal thread holder. I could not get over the difference it made!! ![]() Good suggestion about recording serial numbers. I had problems with a computer once and when had student from the college where I taught come into check it I found out my machine had been switched in a routine checkup and the business has since gone out of business!! ![]() Good Luck *~*~*~* Nancy*~*~*~* " I try to take one day at a time - but sometimes several days attack me at once."
|
User: Sancin
Member since: 02-13-2005 Total posts: 895 |
From: Chrysantha
Date: 03-01-2005, 07:29 PM (4 of 9)
I pay about $150. for a 'tune-up' for my 10000. But he does everything and makes sure it's good to go before I get it back. It usually only takes about 3 days......
Chrys
|
User: Chrysantha
Member since: 09-06-2002 Total posts: 2414 |
From: Kylnne2
Date: 03-02-2005, 03:32 AM (5 of 9)
I might get screamed at for suggesting this LOL but being your machine is a Kenmore would it be less money to take it to your local Sears repair service? I know people prefer dealers but Sears would have the parts of the limited edition that you have, they do carry the Janome parts and it could be less expensive. The only thing is I have heard that if you have no local Sears repair they send the machines out and it could take some time before you get your machine back. I am blessed with a repair service in town. |
User: Kylnne2
Member since: 07-10-2004 Total posts: 629 |
From: teacheraid95
Date: 03-20-2005, 06:34 PM (6 of 9)
I am Totally Frustrated!! So I am begging for suggestions. All of a sudden, the thread breaks while sewing (can hear thread breaking). I remove the material... to rethread the bobbin, the machine will only allow me to do this by going straight to the bobbin, where the thread is showing outside the bobbin (just isn't connecting to thread, when the machine plate is on.) I have even notice (sometimes) that the upper thread is wrapped around the thread spindle, when this happens. I have no clue how. Even tried changing the thread the opposite direction. I oiled the machine (top & bobbin), have adjusted upper tension and bobbin tension. Is there such a thing I need a new bobbin case... It looks fine, it came with the machine. I bought machine new (Walmart~ Brother) about 10 years ago. |
User: teacheraid95
Member since: 11-04-2004 Total posts: 12 |
From: paroper
Date: 03-20-2005, 11:19 PM (7 of 9)
My first thought was that this was a timing problem. After reading the rest of your post I suspect that your thread is on the wrong spindle. Thread that is cross wound (where the thread crosses itself like most European threads) should be placed on a horizontal spindle. Thread that is "straight fed" where the thread goes around and up and down the spool like your bobbin are put on a vertical spindle. Your second spindle could be built in or there may be a place to attach a spindle either in a slot or hole near the area where your other spindle is located. They sometimes fit in a slot at the back of the machine in the general area of the spindle you are using. If you are already following that idea, you probably need to look for a thread net to put over your thread. This will help control the spooling. If you happen to have a multiple spool holder, you can also take your thread through the thread loops across your holder and that will also help slow down the spooling and it can also help control twist in your thread. Your machine probably came with some nets but you may also be able to get some from a florist. Often they come on flowers.
pam
Bernina 200e, Artista V5 Designer Plus, Explorations, Magic Box, Bernina 2000DE & 335 Bernette Serger, Bernina 1530 Sewing Machine, Bernina 1300 DC Overlock (with coverstitch) |
User: paroper
Member since: 02-03-2004 Total posts: 3775 |
From: mamadus
Date: 03-28-2005, 09:18 AM (8 of 9)
you could also try the single spool thread holder that you can get at JOann's// I think it runs $9 or $10. I put it to the right of my ULT and then feed the thread through the regular thread guides along the top of the machine... I agree with Pam.. it sounds like your thread is spooling... MO life is too short, not to explore
|
User: mamadus
Member since: 12-31-2004 Total posts: 492 |
From: paroper
Date: 03-28-2005, 09:29 AM (9 of 9)
If you buy one of those be sure that it is weighted metal...most are cast iron. If you buy one with a plastic base it will move around and fall over on you but the cast ones are great and cost about the same amount!
pam
Bernina 200e, Artista V5 Designer Plus, Explorations, Magic Box, Bernina 2000DE & 335 Bernette Serger, Bernina 1530 Sewing Machine, Bernina 1300 DC Overlock (with coverstitch) |
User: paroper
Member since: 02-03-2004 Total posts: 3775 |
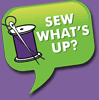
Visit Sew Whats Up for the latest sewing and quilting tips and discussions.
This page was originally located on Sew Whats New (www.sew-whats-new.com) at http://www.sew-whats-new.com/vb/archive/index.php/t-15197.html
Sew Whats Up is hosted by ZenSoft