From: Spinnersilver
Date: 07-23-2006, 07:48 PM (1 of 14)
Does anyone have any helpful hints for monogramming towels? TIA |
User: Spinnersilver
Member since: 07-15-2006 Total posts: 8 |
From: Chrysantha
Date: 07-23-2006, 11:30 PM (2 of 14)
Don't hoop, use sticky...use a topper (washaway), tulle (fabric colored). Make sure you wash the towel before you embroider.( that way if it runs or shrinks, it won't distroy the embroidery.) Chrys
|
User: Chrysantha
Member since: 09-06-2002 Total posts: 2414 |
From: ClareSS
Date: 07-24-2006, 08:50 AM (3 of 14)
I wash the towel first, then hoop a medium weight self-adhesive tear away stabilizer, then float the towel on top of that, making sure it's pressed down well, then float water soluble stabilizer (WSS) ,such as Solvy, on top of it, and pin or basted it down. Also, I use polyester thread rather than rayon, because towels do get washed in hot water and sometimes with bleach. Poly stands up to that much better than rayon thread. |
User: ClareSS
Member since: 04-05-2006 Total posts: 17 |
From: paroper
Date: 07-24-2006, 10:48 AM (4 of 14)
I prefer a washed towel but I do not wash bright or dark towels if they are a gift, red, black and navy towels just don't look as good once they've been washed. However, cotton towels shrink and it is best if you can always do that first. Like several others I do hoop the stabilizer not the towel but I use Aquamesh (sometimes Badgemaster) as my stabilizer. I know that people will tell you that it doesn't work but I've had no problem and my towels are prettier. When I have a dark towel OR a dark design I use black bobbin thread instead of white. I think it looks better. If my design is dense or large I use 2 layers. I use Aquafilm on top.
pam
Bernina 200e, Artista V5 Designer Plus, Explorations, Magic Box, Bernina 2000DE & 335 Bernette Serger, Bernina 1530 Sewing Machine, Bernina 1300 DC Overlock (with coverstitch) |
User: paroper
Member since: 02-03-2004 Total posts: 3775 |
From: bbd
Date: 07-28-2006, 11:25 PM (5 of 14)
I read the articles posted above....I have a brother machine for embroidery ,I tried to follow directions a couple of times. I get frustrated to the point of crying , so, I just gave it up and went on...NOW, I come here to see if anyone else is in my shape???Not apparently..I do not understand the one about "float", she says she just "floats" it...?????????????????Or, " I hoop a wash away stabilizer???Or,"Aqua mesh"???huh????????????????? Does any of you by a miracle live in the upper desert area of S. California????barbara ann ![]() ![]() |
User: bbd
Member since: 09-12-2004 Total posts: 4 |
From: paroper
Date: 07-29-2006, 03:25 AM (6 of 14)
Sorry. I don't. Floating is just putting a loose piece of stabilizer under the hoop (not hooping) and sewing through it. Somebody came up with the "brilliant" idea and a lot of people do i, esp. since a well known personality does it often. Here's my take on that....The purpose of stabilizer is to keep your embroidery from moving/shrinking in the hoop...that is why it is called stabilizer. It is very "stable", doesn't stretch or warp as you stitch. The way that you accomplish that is an age old method called hooping. You very tightly hoop your stabilizer (and sometimes project) and the hoop keeps the design from drawing. The tighter the hooping, the less likely the design will shrink while working. If you compare stabilizer to interfacing, interfacing adds stiffness and or body to a garment. It adds to the life of the garment but does not detract from the original fabric's quality. It is MADE to move like the fabric in the garment so it does stretch and move like the fabric...(one of the reasons that I like the tricot stabilizers with knits(. Interfacing is actually very delicate when used in the garment, something that you might not realize until you get the brilliant idea to try it as an embroidery stabilizer. Interfacing will often shread when used as stabilzer. So...why do you care about the stabilizer in embroidery? Well, the reason is because as your needle "rocks back and forth" making (esp. satin) stitches it pulls the fabric toward the other side so that it tries to pull and tunnel. On top of that, you are doing thousands of stitches (usually) in all directions pulling and grabbing your fabric, pulling it inward. If your fabric is not tightly stabilized, it will pull inward causing puckering. While you are embroidering a lot of the design will overlay the rest and you may not see that it is actually pulling while in the hoop UNTIL you start to do the tiny thin outline embroidery which suddenly appears to be larger than the design leaving gaps. Then when you unhoop, you discover waves and pulls in the design. The reason you have a hoop is to tightly hold your fabric and fight the puckers. So....first off, your stabilizer MUST be hooped to do this...floating a piece of stabilizer under the hoop only adds thickness to the design but does NOT keep your fabric from pulling during the process. That being said there IS one case where floating a piece of stabilizer DOES contribute to the stability of the desgin. When you use one or two pieces of tear away you'll sometimes find that while working the tear away, after being perforated over and over will start to tear on its own before you finish and that can allow the design to pucker...so...if, when you notice this starting to happen you float a piece of stabilizer under the hoop, esp. as soon as the stabilizer starts to tear away, you can sometimes bind the floated stabilier in and reinforce the old stabilizer, sewing it in as you work and keep the design from puckering. This only works as the design begins to tear away. If you start out with the stabilizer there, it will tear away too. How tight? as tight as a drum head. I like to "go hoopless" so that I can get my stabilizer that tight. All fabrics stretch and if I try to do that with the fabric there, I stretch the fabric and then it puckers anyway. "What's hoopless?" You hoop the stabilizer tightly. AS you tighten your hoop you'll find that theh stabilizer will start to buckle as the hoop gets smaller..you need to pull and stretch the stabilizer to keep it tight. Then you spray the stabilizer only with a light spritz of adhesive spray. I use 505 because it doesn't stink and it doesn't gum your needles. Then you gently mark your project for hooping (center...straight of grain, etc), match it and lay it on the hoop. Not only do I have less puckering this way but I find that I have more control over where that project is placed in the hoop. I often fold the project in 1/4s and match the center lines and then just unfold and put it in the hoop (my hoops have the centers marked...I also find that if I match the center lines of the hoop with the grid on my cutting table it is much easier to lay my project in the hoop. The template for your hoops can be matched to your axis and you can lay the template in the hoop to help you get it right too. If I get the project crooked, I lift the whole thing and replace it to keep from getting it off-grain. Once I have the project well placed I either put pins close together on the outside edge all the way around to make sure that it doesn't pull loose There are also some stabilizers that come in different weights and look more like interfacing which also come with and without "glues". Polymesh is a very light weight (feeling) stabilizer that is a little bit translucent and is very strong. Polymesh is a cut away that can be purchased with ir without water or heat activated glues built in doing away with a need for spray adhesives. Many companies make Polymesh and call it "that". Because of its strength and weight and softness it is often used in t-shirts, children's clothing and other delicate placeds. It is one of my favorite stabilizers. It often can be purchased in skin tone, white and black. Aqua Mesh has many of the same characteristics of Polymesh as does (I think) Villene (another common brand). The difference is that they look a bit more like perforated paper when you look at them closely and they dissolve in water completely so that when you are through there is no trace of the stabilizer. Badgemaster is another disolving stabilizer but it looks and feels more like clear plastic. Badgemaster is very strong and commonly used for free standing lace projects (lace that is specially made to self-support itself so when you dissolve the stabilizer you have lace like you might buy in the store from the bolt. With the aqua type stabilizers there does not "have" to be a trace of the stabilizer when the project it washed but you can leave traces in if you want your project to be stiff as in some lace bowls. The trace is only left if you wash it away by hand. While talking about disolving stabilizers, it should be mentioned that there is a topping called solvy or film. It can also come in weights and is used to top a project that has nap or fibers that might "stick up" through your embroidery. It looks like Saran Wrap and disolves completely away. It is delicate enough that it can often be torn away. The sole purpose of this is just to hold down the project so that the nap or thread will be flattened and you can embroider over them. It does not stabilize. People often use tuille or organza in place of this because they do not tend to stick to the foot and because they are permanent. Not all projects need solvy topping to look nice, only those with a nap or elevated texture. There are different types/weights of tear away. Although I don't often use it, I think that tear away can be purchased sometimes with adhesive on the back. Tear away is made so that you don't have to cut it away from the back of your project, you just pull it away and it tears free like a paper. It usually looks like traditional interfacing but it is much stronger and comes in weights like cut away stabilizers. People think of tear away as being stronger than dissolving stabilizers because a part of the stabilizier stays in the project. However, most tear away stabilizers are made to dissolve over time and cannot be counted on to stay in the design forever. As long as it is in the design it does, to an extent support the design though. Unless your design is solid, tear aways will show on the backside for several washings. That is why I do not often use it behind my towels. I like them to be pretty on the back. Besides showing, the other major disadvantage to the tear away is that as you stitch it starts to perforate the tear away and with a lot of repetitive stitching or with a large dense design the tear away will (often) release as the edge is cut free by the needle. The advantage is that when you are through you do not endanger your project with scissors, it just tears away like paper! Nice stuff! Hopefully this answers some of your questions? pam
Bernina 200e, Artista V5 Designer Plus, Explorations, Magic Box, Bernina 2000DE & 335 Bernette Serger, Bernina 1530 Sewing Machine, Bernina 1300 DC Overlock (with coverstitch) |
User: paroper
Member since: 02-03-2004 Total posts: 3775 |
From: onehipgrammy
Date: 08-18-2006, 10:52 PM (7 of 14)
I am also new to Machine Embroidery and have yet attempted towels, but I learned alot reading this thread ... thanks Pam |
User: onehipgrammy
Member since: 08-18-2006 Total posts: 5 |
From: Gaevren
Date: 08-18-2006, 11:51 PM (8 of 14)
Pam, that was a very informative post...answered a lot of questions of mine as well, thank you! ![]() |
User: Gaevren
Member since: 04-07-2006 Total posts: 9 |
From: Dianne Walker
Date: 08-21-2006, 01:21 PM (9 of 14)
Pam - the information you gave on stabilisers was super. I have taken the liberty of printing it our for reference and I am sure it has helped so many of us. As you are obviously an expert - can you possibly tell me the advantages and disadvantages of polyester thread or rayon. I always used Janome thread which just says Acryl with my Janome 10001 but it is very expensive so I started to buy Robison Anton Rayon instead. I then found Jaycotts on the internet in England selling Robison Anton Poly much cheaper than I paid for the Poly at the shop. I noticed it doesn't seem as shinny though. Here in England there are very few places that seem to sell embroidery thread at all and I have to travel miles into Derby to get any. Any help would be greatly appreciated. Thanks Di Dianne
|
User: Dianne Walker
Member since: 01-05-2005 Total posts: 59 |
From: paroper
Date: 08-21-2006, 05:18 PM (10 of 14)
When I first adventured into the area of (home) machine embroidery in 1992, the first threads that I found were rayon. They was lovely, had a lot of shine and bright colors. Overall, that is rayon's claim to fame. It is said not to be as color fast as the poly. On the other hand, poly is said not to be as lovely and shiny as rayon but to be able to withstand bleach and to be stronger thread. In actually, I think that it is more a matter of personal preferance unless you plan to bleach your work (most people don't use chlorine bleach that much anymore on items that would be embroidered). I think that the main thing is to find a brand and product that is compatable with your machine whether it be poly or rayon. Some machines apply a lot of pressure to the threads and they break easier than on others. I am really big on pretty much staying with a brand once you find it. I have a full color assortment of Isacord (poly) and a pretty good assortment of Yenment (metalic). These are the threads that I really like. I have chosen them primarily because I like the texture of the thread and they are compatable with my machines but they are also readily available to me. I have very few problems with the threads in terms of breaking. The reason I recommend pretty much staying with a brand is really very simple. It is easier to convert thread colors from brand to brand than across several brands. If I have PES colors and I wish to convert to Isacord colors it is just a matter of choosing a column and I can get a reasonable conversion. It is also easy to tell when I have a color or when a color is "missing" from my assortment. At the same time, there are a some misc. colors that I also have in Sulky (not really my favorite thread but I still think it is really pretty) rayon because I just like the colors and they do great for special projects. I also have some Madiera threads that are rather special because they are in multi colors that I don't have in the Isacord. pam
Bernina 200e, Artista V5 Designer Plus, Explorations, Magic Box, Bernina 2000DE & 335 Bernette Serger, Bernina 1530 Sewing Machine, Bernina 1300 DC Overlock (with coverstitch) |
User: paroper
Member since: 02-03-2004 Total posts: 3775 |
From: Dianne Walker
Date: 08-23-2006, 01:52 PM (11 of 14)
Thank you Pam once again for such a comprehensive reply. I get your point about sticking to the one brand. I did find that I had quite a few breakages with the Janome thread and find the Robison Anton better for that. I think I will stick with the Robison Anton Rayon as I do like the shiney appearance of the rayon even though for some reason it is quite a lot more expensive than the poly. Thank you very much for your expert help. No doubt there will be more questions further down the line !!!!!! Di Dianne
|
User: Dianne Walker
Member since: 01-05-2005 Total posts: 59 |
From: bridesmom
Date: 08-23-2006, 10:48 PM (12 of 14)
One more question on embroidering towels. My DD gave me some black towels to do some white lettering on. Should I still use the black bobbin thread?
Laura
Tickled pink with my Innovis 4000D |
User: bridesmom
Member since: 01-21-2004 Total posts: 2026 |
From: paroper
Date: 08-23-2006, 11:43 PM (13 of 14)
It is strictly personal taste. I use black bobbin thread when using either a dark design or if I am using a dark medium (towels for instance). Personally I just think it looks a little better.
pam
Bernina 200e, Artista V5 Designer Plus, Explorations, Magic Box, Bernina 2000DE & 335 Bernette Serger, Bernina 1530 Sewing Machine, Bernina 1300 DC Overlock (with coverstitch) |
User: paroper
Member since: 02-03-2004 Total posts: 3775 |
From: mamadus
Date: 08-25-2006, 02:08 PM (14 of 14)
I think everybody develops a method that works well for them... I happen to be one of those folks who uses tear away on towels... I have never had a problem with it... I do use the hoopless method and 505, and normally I will use either solvy or tulle as a topper, depending on the intricacy of the design... its good to try different methods and find what you feel most comfortable with and what works best for you... I also will occasionally "float" stabilizer under a design, especially if its a particularly dense design... and my personal preference is to use basting stitches as opposed to pins, when going "hoopless". Since I primarily use Embird, which gives you the option to add basting stitches to your design, i find htat's more convenient than running hte risk of bumping into pins during the embroidery process... in hte end, you just have to jump in and experiment and find what works best for you.... as the old saying goes... "there's more than one way to skin a cat" just my 2 cents... MO life is too short, not to explore
|
User: mamadus
Member since: 12-31-2004 Total posts: 492 |
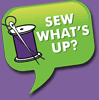
Visit Sew Whats Up for the latest sewing and quilting tips and discussions.
This page was originally located on Sew Whats New (www.sew-whats-new.com) at http://www.sew-whats-new.com/vb/archive/index.php/t-19704.html
Sew Whats Up is hosted by ZenSoft