From: Dianne Walker
Date: 05-16-2007, 02:51 PM (1 of 13)
Hi everyone I am sure there is someone out there who can help with my current problem. I have been asked to embroider a logo for a riding school onto childrens' polo shirts. I have found a super design of a girl on a pony and have added the name fine. The problem is that the design is quite dense and the polo shirts fairly small so I hooped a tear away sticky stabiliser and also floated some cut away underneath for added support. It stitched out reasonably well but had a few thread breakages due to the density. The main problem seems to be that I cut round the cut away and the sticky is so well and truely stuck to the shirt that it it is virtualy impossible to move. Is there a better method for stabilising this project or how do I remove the sticky tear away? It is not really possible to hoop the shirt because of the front opening with the buttons and also the sleeve seem as these are quite small sizes, 7 to 8 year olds upwards. Any ideas would be very much appreciated. Many thanks Dianne Dianne
|
User: Dianne Walker
Member since: 01-05-2005 Total posts: 59 |
From: MotherInLaw
Date: 05-16-2007, 10:34 PM (2 of 13)
Hi Dianne, I always use the spray for embroidery on things like this. Hoop the stablizer, there are some really good polymesh stablizers for knits out there that are iron on but I use them without ironing them on I just use the spray to stick the shirt down . I spray the hoop and then stick the shirt to the top of the stablizer. When finished the spary allows you to pull it right up and all that is stuck to the shirt is the part that is sewn on. It can be a little tacky but after it's washed it's all gone.
I'm regressing back into my youth, I just have to figure out how I'm going to convience my body to come along with me.
|
User: MotherInLaw
Member since: 06-25-2005 Total posts: 1118 |
From: Dianne Walker
Date: 05-17-2007, 06:04 AM (3 of 13)
Hi Sue Long time - no hear - hope you are well and happy. Back to the plot - thanks for your help. When you say you spray the hoop, do you mean all over the surface of the stabiliser or just round the edge to hold the shirt to the hoop? I can see that if it hold with just a spray round the edge I could still float some extra underneath if needed and still be able to remove the sprayed on stabiliser. Am I making it clear or more confusing? Dianne Dianne
|
User: Dianne Walker
Member since: 01-05-2005 Total posts: 59 |
From: paroper
Date: 05-17-2007, 12:03 PM (4 of 13)
Dianne, forget the floating stuff...that is not what you need. First of all, never use a tear away stabilizer with a knit. Tear away puts stress on the stitching and it runs the risk of pulling the design apart just taking the stabilzer away. Also, any stabilizer that is NOT permanent will not support the design in a knit, the lighter the design the worse it is so that someone when just putting on the shirt can cause the design to litterly come apart. You have the right idea with the sticky "stuff" but you are using the wrong stabilzier. Hoop 2 LAYERS of Polymesh. Hoop them tightly. Spray them with 505 or another reputable spray. SPRAY THEM ALL OVER, not just on the edges. Lay your design on the sprayed stabilizer and if you have it, use your basting template (many machines which do not have these built into the machine will have them for download on their site). This further keeps your shirt from shifting and coming loose while you are working. If your do not have access to the basting design, then pin closely all around the inside of the hoop well out of the way of your design...and I mean pin baste one right after the other. The spray will keep your knit from moving and puckering as you work. Now let's talk about what you are attempting to do and what stabilizer is for. Stabilizer is not like interfacing. It does not just provide a framework for your design, add thickness, stiffness, etc like interfacing. Do not use interfacing in place of stabilizer as it also tends to pull apart. Stabilizer is very strong and can resist pull where interfacing is meant to add stiffness and body to a garment, stabilzer only keeps the design from pulling into itself as you stitch. ONLY THE STABILIZER which is hooped can resist the pull of the machine. Stabilizer that is laying under the hoop does not resist this. The only time that I float anything under the hoop is when I am using tear away (always on a woven fabric) and it starts to pull loose when I am stitching. A small piece of floated stabilizer can help strengthen the tear and bridge the gap to keep it from increasing. Each time you take a stitch, the thread try to pull the thread into itself (creating pucker). The purpose of the stabilzier is to provide a solid backing to keep the machine from puckering the design so it has to be strong and solid. In most cases, the job of the stabilizer, unlike that of interfacing is finished when the design is through. The exception to that rule is when you are doing knits. Because knits will stretch and pull with body movement, you must ALWAYS use a cut away with KNITS. They provide a solid backing so that the design itself does not stretch when the knit pulls away. You can use tear away and water soluble on wovens, but cut away is always the most stable of the stabilziers and it must be used on stretchy fabrics. pam
Bernina 200e, Artista V5 Designer Plus, Explorations, Magic Box, Bernina 2000DE & 335 Bernette Serger, Bernina 1530 Sewing Machine, Bernina 1300 DC Overlock (with coverstitch) |
User: paroper
Member since: 02-03-2004 Total posts: 3775 |
From: Dianne Walker
Date: 05-17-2007, 03:17 PM (5 of 13)
Thank you Pam for taking the trouble to write such a comprehensive reply. I have printed it out for future reference. I am sure you will think I am completely stupid - but what exactly is Polymesh? I have got some Sulky Sheer Cut-Away which says it is textured non woven nylon. Will that be any good to use for this project do you think? All the rest I have at the moment are either iron on (the Janome one) or various sticky ones where you peel off the backing or wet the surface to stick. I have got a 505 spray though. I find this stabilising a bit of a mine field. Looking on the internet there are so many, with a lot all claiming to do the same thing, that I really don't know where to start. If you could possibly explain a little more about the uses of the various types and weights with perhaps the name they are purchased under I can track them down on the net. I am sure this would be very helpful for all of us in the "novice" category. I think you should write a book Pam with all the advice I read from you when answering people's questions. I am sure it would be a best seller!!! Many many thanks, Dianne PS I live in England and only have one shop in my nearest city that stocks anything to do with Machine Embroidery and they are very limited. They told me when I got my machine (Janome MC 10001) that the only stabilisers I needed where the iron on one they sell and a water soluble one as a topping for towels. I think they misled me somewhat. Dianne
|
User: Dianne Walker
Member since: 01-05-2005 Total posts: 59 |
From: paroper
Date: 05-17-2007, 07:39 PM (6 of 13)
Ok, so I opened this just before I left to pick up my dgd from school this afternoon and I've been thinking about it ever since....so let's give it a try. First of all, let's establish what we are talking about here. Interfacing is not stabilizer, as I mentioned previously. Interfacing is used to give body to the garment, to stiffen some areas such as saggy necklines, to add stabilizity and strength to others, such as button holes. Interfacing is put in the garment to extend the life of the garment, and it also gives the garment a more expensive look. A good interfacing will will move with the body and in time will take on the shape of the person wearing the garment. In most situations, it should be matched to the weight of the fabrics used. In some cases, more than one type of interfacing is used in a garment and it may even be used as an interlining in some cases. We speak of stabilizing a garment which is confusing but we actually add interfacing to stabilize a garment. One way to tell a non-woven interfacing from stabilzier is if you pull it from side to side, the interfacing will shread, unlike a stabilizer. Stabilizers can be woven, like cotton organza (still one of my favorites, but hard to find here), non woven or pressed like Pellon or it can be knit or tricot which is great for many different types of fabrics (we'll come back to this one). When a stabilizer is put in a garment, it's "duty" is just beginning. Stabilizer is a whole different type of critter. When a machine stitches back and forth, it pulls the fabric together and attempts to tunnel. If this works, your fabric and design will pucker. In many cases, if the fabric is poorly hooped or stabilized, the outlines of the design will be "off" in places. Most often you'll be able to tell because the design may be right in some places, off in others. While you match the weight of interfacing to sewn fabric, you also match the weight of the stabilizer to the fabric to which you are applying machine embroidery. The stabilizer MUST be heavy enough to hold the fabric in place and this usually means that the weight or combined weights of the stabilizer you use should be slightly heavier than the fabric which it is trying to tame. Many people will say that you don't need to stabilize heavy fabrics like denium but in fact, there is clearly a difference between denium that is stabilized and denium which is not. All fabrics (with which I have come in contact) has a bias which has some stretch. That bias must be controlled. I have yet to find a stabilzer which is woven. For the most part it is some sort of pressed fiber, often with a pattern like Poly Mesh, or it is a film of some type. There are 2 basic types of stabilizer, each of which contains several weights: Cut away, Tear away and Water soluble (including films). Cut away and tear away stabilizers can be found with and without adhesive. The built-in adhesives can be heat activated, water activated or they can be self-sticking. Self-sticking tear away looks like fly paper (yuck). Water solubable stabilzers can be a mesh stablizer or it can be film. Some of the films are very light weight and they go all the way to Badgemaster which feels like a heavy grade of (nearly) clear plastic and is great for things like Free standing lace. Mesh stabilziers are about the weight of Poly Mesh (cut away) and come under several brands...most popular of which are Villene and Aqua Mesh. For a long time I had a hard time telling Poly Mesh from Aquamesh. First I found that I could dampen my finger and feel the edge. Aquamesh would become sticky but it also looks like a sheet of something very flat with pin pricks where you can see a weave pattern in Polymesh. There is another type of film stabilizer that is seldom mentioned. While water soluble stabilizers are removed by water, there is a heat soluble stabilizer which can be used on items which can not take water or would spot. I have some, haven't tried it. The stabilizer, when properly used, is said to dissolve to ash. Ok, so how do you determine which fabrics for which stabilizers? Well, as mentioned before, the stabilizer should be slightly heavier than the fabric with which it will be used; but many fabrics are heavier than the stabilizer, so what do you do? When I first started out, I was having a lot of pucker problems. The magic key was that I needed two layers of almost any stabilizer. Problem 99% solved. Cut away stabilizers are the most reliable of all stabilizers. When I have a project where the stabilizer will be hidden, I always use a cut away, regardless of the type of fabric. CUT AWAY MUST ALWAYS BE USED ON KNITS of all kinds. As stated above, the designs on knits can be pulled apart by the simple action of putting the garment on, washing the garment and it getting tangled in the process, or even a garment that is a little tight on the wearer so you do not want a stabilizer that will disappear when it is finished. Tear away stabilizers can be used with woven fabrics. I don't often use tear away because it leaves residue in the garment when you tear it out and it is scratchy. As you sew, tear away perforates which aids in its removal. As you remove the tear away, you put your finger on the stitching and gently tear. To yank or pull is to loosen the stitching. Now, the next thing I'm going to say generally makes tear away fanatics angry but it is true and it came straight from the horses' mouth at OESD whose name appears on many of these stabilziers! Many people think that tear away supports the stitches on an item even when you tear away the outside stabilizer. In fact, the tear away stabilizers continue to dissolve every time they are washed AND just as the perforate on the outside edge of the design, they also perforate on the inside and the inside perforations are much closer together and finer than the outside so that by the time you finish, the internal stabilizer does NOT support the stitching. Another thing I don't like about the tear away is that often it will start to seperate before you are finished with your item. This is the one case where I float stabilizer. If this happens to you, take a piece of tear away stabilizer, spray with adhesive, if you have it and patch the hole while it is small. It will reinforce the tear and the continued stitching will cause it to bridge the opening and stop further damage. Water soluble stabilizers come in weights...from the very very light used on top of items to medium weight to very heavy weight films and then there are the meshes. Water soluble (my favorite after cut aways) are pretty much interchangable with tear away. In most cases, light to medium weight films are used on the top of things WITH NAP like long pile velvet (although I like to do velveteen without film), loopy towels, some fleece. The idea is that the film allows you to stitch the item without the thread fibers interferring and getting caught in the process. Some people talk about the stitches sinking into the garment...that is called tension. It never hurts to use a film but it is expensive and I don't see a reason to use it all the time unless it is needed. When people talk about everything looking better with it, I think much of that is psycological. In some cases it is better to use organza or tuille in place of the film on top of the item because it doesn not wash away. These fabrics can also add interest to the item. In a pinch, virtually any WSS (water soluble stabilizer) can be used on top of the garment. I use 2 layers of Aquamesh on the bottom of towels rather than tear away because when it is gone, it is gone. I like to use the hoopless method for most things. It allows for easier/better placement and allows you to get a good, tight, drum head seal on your stabilizer in the hoop without pulling the fabric. It is very important that the fabric not be pulled or stretched. You say that you have several types of adhesive stabilzers. There is no problem using these. You probably have a nice, light soft water or heat activated stabilizer for your t-shirts. That is just fine to use. If you do not, a good light weight cut away mesh stabilizer (2 layers) will work well. If you use the non-adhesive stabilizer and 505, use a very LIGHT SPRITZ to apply the spray to your stabilizer, let it set a few seconds, then center your fabric on the hoop. Now, even with the spray or adhesive, the weight of the garment and the pull of the hoop movement can cause the garment to loosen on the hoop. For this reason, you will want to baste it to the stabilizer. Basting can either be by machine or it can be by pin basting...now, pin basting is not just 4-5 pins places stratigically around the hoop, it is pins, one after the other framing the hoop, well out of the area of stitching, right next to the frame. Longer pins are better for this and the sewn basting is better. To cover the roughness of the stitches, you can use a layer of TRICOT or knit INTERFACING (not stabilizer) ironed to the back of the garment. pam
Bernina 200e, Artista V5 Designer Plus, Explorations, Magic Box, Bernina 2000DE & 335 Bernette Serger, Bernina 1530 Sewing Machine, Bernina 1300 DC Overlock (with coverstitch) |
User: paroper
Member since: 02-03-2004 Total posts: 3775 |
From: paroper
Date: 05-17-2007, 07:55 PM (7 of 13)
Free Standing Lace (FSL)..Badgemaster or two layers of Villene or Aqua Mesh T-shirts...2 layers polymesh batiste or light weight cotton...2 layers polymesh (best to hoop if possible), #9 or #10 sharp needle towels...2 layers polymesh or 1 layer badgemaster denium, canvas, uphostery type fabrics...two layers xtra heavy cut away sweat shirts..I prefer 2 layers of heavy cut away The two layers of xtra heavy cut away on heavy fabrics is good for about any type of design but you may need to add a layer on some of the lighter fabrics if the design is extra heavy, including adding a layer to t-shirts. If your t-shirts have too heavy a design they will pyramid. I hope this is enough information to get you going....Good luck on this venture! Polymesh is marketed under that name by many mfgs but most make a similar product. I haven't looked at many of the Sulky products. Those that I have looked at seemed a little light. I'd test that stabilizer on an old T and see if you need an extra layer. With a little practice, you'll be up and going in no time!!! pam
Bernina 200e, Artista V5 Designer Plus, Explorations, Magic Box, Bernina 2000DE & 335 Bernette Serger, Bernina 1530 Sewing Machine, Bernina 1300 DC Overlock (with coverstitch) |
User: paroper
Member since: 02-03-2004 Total posts: 3775 |
From: MotherInLaw
Date: 05-17-2007, 11:40 PM (8 of 13)
Hi Dianne, Long time no see is right. How have you been? I'm going to be grandma again!!! Another girlie. That Janome still purring I see. ![]() I'm regressing back into my youth, I just have to figure out how I'm going to convience my body to come along with me.
|
User: MotherInLaw
Member since: 06-25-2005 Total posts: 1118 |
From: Dianne Walker
Date: 05-20-2007, 01:38 PM (9 of 13)
Phew!!! Pam first - what a super amount of information. You really are a star and thank you so very much. I feel so much better informed now and hope that some of the designs I have done in the past and found that when it stitches the final outline it ruins the lot, will be a thing of the past too. I am so grateful for all the time you must have taken with my question and I expect there are many many others out there who will have also benefitted from your reply. I was interested to read about the iron on to cover the roughness of the stitches. I did a T shirt a while ago for my young grandson and although he loved it he said it was very "itchy" so I will try and track some of that down as well I do wish we had as many outlets in England as I know you have in America. Thanks again Pam - extremely grateful. Di Now Sue - good to hear from you again and congratulations on the new grand daughter. What is her name? I also became a grandparent again some 12 weeks ago. My son's wife had a second little boy who is of course a grand little chap as they always are. They have called him Myles. They came round to see us this morning so I had a lovely long cuddle!!!. Hope you are keeping well and look forward to hearing from you again soon. Take care and many thanks Di Dianne
|
User: Dianne Walker
Member since: 01-05-2005 Total posts: 59 |
From: bridesmom
Date: 05-21-2007, 07:26 PM (10 of 13)
Wow, got to love you Pam. When you write your book, can I have a copy???? What great tips!! Takes a lot of the guesswork out of stabilizing for me!! Thanks!![]() Laura
Tickled pink with my Innovis 4000D |
User: bridesmom
Member since: 01-21-2004 Total posts: 2026 |
From: paroper
Date: 05-21-2007, 07:32 PM (11 of 13)
You're welcome. Now, once you get it "down" remember that you'll develop your own techniques and style. There is always more than one way to do something!
pam
Bernina 200e, Artista V5 Designer Plus, Explorations, Magic Box, Bernina 2000DE & 335 Bernette Serger, Bernina 1530 Sewing Machine, Bernina 1300 DC Overlock (with coverstitch) |
User: paroper
Member since: 02-03-2004 Total posts: 3775 |
From: Dianne Walker
Date: 05-27-2007, 08:21 AM (12 of 13)
Pam I have managed to complete a couple of the polo shirts I first asked the question about and have had much more success now following your sound advice. Cut away stabiliser has proved to be much much better and I thank you so much for all the trouble you have taken. Kind regards Dianne Dianne
|
User: Dianne Walker
Member since: 01-05-2005 Total posts: 59 |
From: paroper
Date: 05-27-2007, 02:56 PM (13 of 13)
Glad it worked well for you!
pam
Bernina 200e, Artista V5 Designer Plus, Explorations, Magic Box, Bernina 2000DE & 335 Bernette Serger, Bernina 1530 Sewing Machine, Bernina 1300 DC Overlock (with coverstitch) |
User: paroper
Member since: 02-03-2004 Total posts: 3775 |
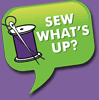
Visit Sew Whats Up for the latest sewing and quilting tips and discussions.
This page was originally located on Sew Whats New (www.sew-whats-new.com) at http://www.sew-whats-new.com/vb/archive/index.php/t-22409.html
Sew Whats Up is hosted by ZenSoft